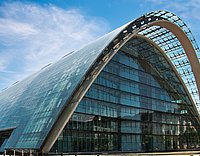
May we present: “Obsoletely”, an interactive portal for replacement parts. Our experts Lukas Jacob and Nizar Manzli from the Körber Business Areas Pharma and Digital explain how it works and helps customers prevent machine downtime.
Pharma
May we present: “Obsoletely”, an interactive portal for replacement parts. Our experts Lukas Jacob and Nizar Manzli from the Körber Business Areas Pharma and Digital explain how it works and helps customers prevent machine downtime.
Körber builds inspection machines for the pharmaceutical industry, among other products. What happens if something breaks down at one of your customers’ facilities?
Lukas Jakob: The company may have to halt production — and for the kind of companies that we supply, that can get very expensive very fast. That’s why our customers expect us to provide replacement parts very quickly.
That should be doable, shouldn’t it?
Lukas Jakob: It should be, yes. Often, though, it’s just when a part is needed that suppliers will tell us that this or that replacement part isn’t available.
And what do you do then? Offer an alternative to the component that’s out of stock?
Lukas Jakob: That sounds good, but then the machine would have to be down for a while, because it would have to be modified. That’s a lot of lost time.
And that’s where the colleagues at Digital came into play?
Nizar Manzli: Yes, exactly. We thought about how we could make replacement parts management more effective. We talked to a lot of our colleagues and to experts from all of our business areas, and we quickly saw that almost all companies face these same challenges. And so it seemed natural to turn this into a joint project.
Which then became Obsoletely. What does the term mean, and what does it involve?
Nizar Manzli: “Obsoletely” comes from the word “obsolete,” meaning out of date. It’s a kind of Wikipedia for replacement parts — a portal where you can find out everything you want to know about spare parts. It allows everyone — our customers, our suppliers and us ourselves — to find everything we need through this one interface.
You’re describing it as an interface. Does that mean the information flows in both directions?
Nizar Manzli: Yes. Our customers upload all the components of their machines, and then our system automatically checks the current status of those parts at the manufacturers. That way we’re kept informed of any irregularities that could occur in the future. Using this information, we generate documents that include details such as the expected service life of individual components. This keeps all of the parties involved up to date. And here’s the best thing: All it takes is a click for our customers to call up the information.
Lukas Jakob: Since we and our customers keep an eye on the life expectancy of individual parts, we can make sure new supplies become available in good time. As a result, our customers are better prepared for a possible replacement. This means that Obsoletely greatly helps to prevent machine downtimes due to a lack of components that are no longer produced. And in certain situations, we’ll also tell our customers whether it would make sense to stock up on spare parts one last time or retrofit their machines now. This can be the case, for example, if we know that certain components will not be manufactured much longer.
lOur customers expect us to provide replacement parts very quickly.r
Lukas Jakob, Körber Business Area Pharma
But at some point, the spare parts aren’t going to be available at all. What happens then?
Lukas Jakob: That’s an opportunity for us, too. If parts are no longer available, we can modify the customer’s machine. In other words, we can modify it so it can accept the next generation of the spare part.
Nizar Manzli: We also want to be able to predict the life expectancy of individual parts, technically and organizationally. For example, if a replacement part from company XY is only kept in stock for 15 years before production is halted, then we’ll know that and notify our customers of this fact.
Lukas Jakob: We had a case like this with industrial cameras, a great many of which are installed in some machines. The manufacturer had informed us at short notice that it was dropping the cameras from its lineup. Then, when precisely these cameras broke down at one of our customers’ facilities, we had already stocked up, and we were able to provide replacements right away.
If it always goes that fast, that should increase the effectiveness of the machines too.
Nizar Manzli: It does that indeed. Our objective is to increase equipment effectiveness by up to 30 percent by reducing machine downtime. And we’re on the right track.
lObsoletely is a kind of Wikipedia for replacement parts — a portal where you can find out everything you want to know about spare parts.r
Nizar Manzli, Körber Business Area Digital
Wikipedia is getting larger and larger. How do things look at Obsoletely?
Nizar Manzli: The situation is similar. We started with Obsoletely in mid-2019. At the beginning, it was very helpful to be able to point to our huge network in the Körber Group. And of course the more customers we have, the better the prices we can get, and thanks to that and our greater visibility in the market, we gain still more customers. With every customer that uploads its components, the system is growing all the time, and that benefits everyone: There are more manufacturers for our customers, and more customers for the manufacturers.
How many replacement parts does Obsoletely have information on?
Nizar Manzli: At the beginning, it contained information on a few thousand parts. Now, it’s already more than a million components. Whenever new ones appear on the market, we’re informed of this automatically via the websites of the manufacturers and suppliers. A bot — a computer program — is constantly at work collecting this information with its algorithm. Every day, all day long, and all night long, it’s busy working for our customers and suppliers.
Insights shows the entire spectrum of Körber, what we do and how we do it: We give our view of exciting developments and trends, as well as innovations and technologies. We also highlight personalities who drive Körber forward every day with their entrepreneurial spirit and new ideas - always to the benefit of our customers. In this section, you’ll find inspiring content concerning our topic Tech.
Learn more