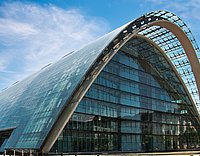
Digital handbooks instead of thick folders
One impressive example of the clever use of digital helpers is paperless assembly. This avoids mountains of paper and and reduces the impact on the environment. The second, equally important, effect is a huge increase of efficiency in the production process. “In paperless assembly, all the information our employees need for the production of our highly sophisticated machines is provided to them in digital form at a mobile workstation,” explains Schweitzer.
This is a man-sized, ergonomically designed, and mobile workstation consisting of a computer, a display, a keyboard, and a mouse. It stands on rollers that make it easy to move. A powerful rechargeable battery guarantees independence from the power grid.
The workstation enables assembly workers to access all the relevant information they need directly in the workshop. Previously they had to browse through thick paper folders, but now the digital handbooks, safety data sheets, and documentation are always close at hand – and come without any weight. In addition, employees can call up 3-D diagrams, document quality inspections, and check to see whether all the components they need are available. In case an assembly worker ever needs to “descend into the depths” of a machine, he can take along a handy tablet so that he’d still have all documents on hand.