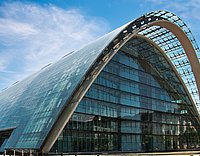
In Hungary, Hauni is using innovative solutions to develop production processes towards the smart factory. The company’s customers are benefiting from its increased efficiency whilst keeping the high quality.
Ferenc Brozovácz puts on his welding helmet, checks the ventilation hose, and chooses his first welding spot. The piece of steel he’s working on stands on a workbench. Behind him, on a touchscreen, are glowing key figures, construction drawings, and DIN standards. “Ferenc can check this display at any time to find out where he needs to make the next weld spo — or to get other information that’s relevant to his job,” says Beáta Szolnok. She’s one of the experts in the Lean program FAST at the Hauni plant in Pécs, Hungary. E-documentation — the availability of important electronic documents directly at the workplace — is one of several dozen FAST projects in Pécs. It’s a crucial step toward paperless production processes. Today more than 300 employees at this plant are working with it.