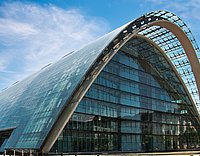
Robots that navigate with 3D cameras and sensors
The big innovation of AMRs lies in the ‘A’ part: ‘autonomous.’ In contrast to most robots used in warehouses in the past, they don’t require any permanently installed rails or magnetic tracks. Instead, they navigate through buildings using digital maps, 3D cameras, and advanced sensors. They move out of the way of people and other robots without interrupting their trip. The job of retrieving products from, or placing them in, bays is often still done by people, the pickers. “The robots save them the effort of unnecessarily going back and forth in the aisles,” explains John Santagate, Vice President Robotics in the Business Unit Software at Körber Supply Chain. “That can make up more than half of the working time — which is time they can put to better use some other way.” This makes logistics processes much more efficient.
AMRs also fundamentally change the relationship between people and machines. “Robots and employees now work hand in hand,” says Dirk Teschner. His responsibilities in the Körber Business Area Supply Chain include introducing AMRs on the European market. “Until now, people and robots have performed different jobs in warehouses,” says Teschner. In extreme cases, robots have been permanently installed in one place, behind bars or other safety barriers. “Now,” says Teschner, “they're leaving these cages.” That raises warehouse management to a new level. Warehouse operators can deploy the robots more flexibly and give them much more complex tasks.